หลักการเคลือบผิวด้วยการระเหยด้วยสุญญากาศ
1、อุปกรณ์และกระบวนการทางกายภาพของการเคลือบผิวด้วยการระเหยด้วยสุญญากาศ
อุปกรณ์เคลือบการระเหยด้วยสุญญากาศส่วนใหญ่ประกอบด้วยห้องสุญญากาศและระบบอพยพภายในห้องสุญญากาศมีแหล่งกำเนิดการระเหย (เช่น เครื่องทำความร้อนการระเหย), ซับสเตรตและโครงซับสเตรต, ฮีตเตอร์ซับสเตรต, ระบบไอเสีย ฯลฯ
วัสดุเคลือบถูกวางไว้ในแหล่งกำเนิดการระเหยของห้องสุญญากาศ และภายใต้สภาวะสุญญากาศสูง แหล่งกำเนิดการระเหยจะถูกให้ความร้อนเพื่อให้ระเหยเมื่อช่วงอิสระโดยเฉลี่ยของโมเลกุลของไอระเหยมีขนาดใหญ่กว่าขนาดเชิงเส้นของห้องสุญญากาศ หลังจากที่อะตอมและโมเลกุลของไอฟิล์มหนีออกจากพื้นผิวของแหล่งกำเนิดการระเหย แทบจะไม่ถูกกีดขวางจากการชนกันของโมเลกุลหรืออะตอมอื่น และเข้าถึงพื้นผิวของวัสดุที่ต้องการเคลือบได้โดยตรงเนื่องจากพื้นผิวมีอุณหภูมิต่ำ อนุภาคไอของฟิล์มจึงควบแน่นและก่อตัวเป็นฟิล์ม
เพื่อปรับปรุงการยึดเกาะของโมเลกุลระเหยและซับสเตรต ซับสเตรตสามารถเปิดใช้งานได้โดยการให้ความร้อนที่เหมาะสมหรือการทำความสะอาดด้วยไอออนการเคลือบผิวด้วยการระเหยด้วยสุญญากาศต้องผ่านกระบวนการทางกายภาพต่อไปนี้ ตั้งแต่การระเหยของวัสดุ การขนส่ง ไปจนถึงการทับถมเป็นฟิล์ม
(1) ใช้วิธีต่างๆ ในการแปลงพลังงานรูปแบบอื่นเป็นพลังงานความร้อน วัสดุฟิล์มจะได้รับความร้อนเพื่อระเหยหรือระเหิดเป็นอนุภาคก๊าซ (อะตอม โมเลกุล หรือกลุ่มอะตอม) ด้วยพลังงานจำนวนหนึ่ง (0.1 ถึง 0.3 eV)
(2) อนุภาคก๊าซออกจากพื้นผิวของฟิล์มและถูกเคลื่อนย้ายไปยังพื้นผิวของวัสดุพิมพ์ด้วยความเร็วที่กำหนดในการเคลื่อนที่ในแนวเส้นตรงโดยไม่ชนกัน
(3) อนุภาคก๊าซที่มาถึงพื้นผิวของสารตั้งต้นจะรวมตัวกันและเกิดนิวเคลียส จากนั้นจะเติบโตเป็นฟิล์มโซลิดเฟส
(4) การจัดระเบียบใหม่หรือพันธะเคมีของอะตอมที่ประกอบกันเป็นฟิล์ม
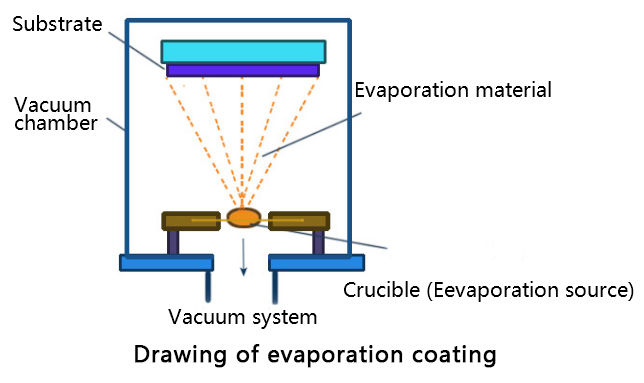
2、 การทำความร้อนด้วยการระเหย
(1) ต้านทานการระเหยของความร้อน
การระเหยด้วยความร้อนด้วยความต้านทานเป็นวิธีการให้ความร้อนที่ง่ายและใช้บ่อยที่สุด โดยทั่วไปใช้ได้กับวัสดุเคลือบผิวที่มีจุดหลอมเหลวต่ำกว่า 1500 ℃ โลหะที่มีจุดหลอมเหลวสูงในรูปของลวดหรือแผ่น (W, Mo, Ti, Ta, โบรอนไนไตรด์ ฯลฯ) มักจะทำให้เป็นรูปร่างที่เหมาะสมของแหล่งกำเนิดการระเหย เต็มไปด้วยวัสดุการระเหย ผ่านความร้อนของจูลของกระแสไฟฟ้าเพื่อหลอม ระเหย หรือระเหิดวัสดุชุบ รูปร่างของแหล่งกำเนิดการระเหยส่วนใหญ่ประกอบด้วยเกลียวหลายเส้น รูปตัวยู คลื่นไซน์ , แผ่นบาง, เรือ, ตะกร้ากรวย ฯลฯ ในขณะเดียวกันวิธีการนี้ต้องการให้วัสดุต้นทางระเหยมีจุดหลอมเหลวสูง, ความดันไออิ่มตัวต่ำ, คุณสมบัติทางเคมีที่เสถียร, ไม่มีปฏิกิริยาทางเคมีกับวัสดุเคลือบที่อุณหภูมิสูง, ทนความร้อนได้ดี ความหนาแน่นของพลังงานเปลี่ยนแปลงเล็กน้อย ฯลฯ ใช้กระแสสูงผ่านแหล่งกำเนิดการระเหยเพื่อให้ความร้อนขึ้นและระเหยวัสดุฟิล์มโดยการให้ความร้อนโดยตรง หรือใส่วัสดุฟิล์มลงในถ้วยใส่ตัวอย่างที่ทำจากกราไฟต์และทนต่ออุณหภูมิสูงบางประเภท ออกไซด์ของโลหะ (เช่น A202, B0) และวัสดุอื่นๆ เพื่อให้ความร้อนทางอ้อมระเหย
การเคลือบต้านทานการระเหยด้วยความร้อนมีข้อจำกัด: โลหะทนไฟมีความดันไอต่ำ ซึ่งยากต่อการสร้างฟิล์มบางองค์ประกอบบางอย่างง่ายต่อการสร้างโลหะผสมด้วยลวดความร้อนไม่ใช่เรื่องง่ายที่จะได้องค์ประกอบที่สม่ำเสมอของฟิล์มโลหะผสมเนื่องจากโครงสร้างที่เรียบง่าย ราคาต่ำ และการใช้งานง่ายของวิธีการระเหยด้วยความร้อนแบบต้านทาน จึงเป็นการประยุกต์ใช้วิธีการระเหยโดยทั่วไป
(2) การระเหยด้วยความร้อนของลำแสงอิเล็กตรอน
การระเหยของลำแสงอิเล็กตรอนเป็นวิธีการระเหยของวัสดุเคลือบโดยการทิ้งลำแสงอิเล็กตรอนที่มีความหนาแน่นพลังงานสูงโดยใส่ไว้ในถ้วยใส่ตัวอย่างทองแดงที่ระบายความร้อนด้วยน้ำแหล่งกำเนิดการระเหยประกอบด้วยแหล่งกำเนิดการปลดปล่อยอิเล็กตรอน แหล่งพลังงานการเร่งด้วยอิเล็กตรอน ถ้วยใส่ตัวอย่าง (โดยทั่วไปคือถ้วยใส่ตัวอย่างทองแดง) ขดลวดสนามแม่เหล็ก และชุดน้ำหล่อเย็น เป็นต้น ในอุปกรณ์นี้ วัสดุที่ให้ความร้อนจะวางอยู่ในน้ำ - ถ้วยใส่ตัวอย่างที่เย็นลง และลำแสงอิเล็กตรอนจะทิ้งระเบิดเพียงส่วนเล็กๆ ของวัสดุ ในขณะที่วัสดุที่เหลือส่วนใหญ่ยังคงอยู่ที่อุณหภูมิต่ำมากภายใต้ผลกระทบที่เย็นลงของถ้วยใส่ตัวอย่าง ซึ่งถือได้ว่าเป็นส่วนที่ถูกทิ้งระเบิดของถ้วยใส่ตัวอย่างดังนั้น วิธีการให้ความร้อนด้วยลำแสงอิเล็กตรอนสำหรับการระเหยจึงสามารถหลีกเลี่ยงการปนเปื้อนระหว่างวัสดุเคลือบผิวและวัสดุต้นกำเนิดการระเหยได้
โครงสร้างของแหล่งกำเนิดการระเหยของลำแสงอิเล็กตรอนสามารถแบ่งออกเป็นสามประเภท: ปืนตรง (ปืน Boules) , ปืนวงแหวน (เบี่ยงเบนด้วยไฟฟ้า) และปืน e (เบี่ยงเบนแม่เหล็ก)ถ้วยใส่ตัวอย่างตั้งแต่หนึ่งถ้วยขึ้นไปสามารถวางในเครื่องระเหยสาร ซึ่งสามารถระเหยและสะสมสารต่างๆ หลายชนิดพร้อมกันหรือแยกกัน
แหล่งกำเนิดการระเหยของลำแสงอิเล็กตรอนมีข้อดีดังต่อไปนี้
①ความหนาแน่นของลำแสงสูงของแหล่งกำเนิดการระเหยด้วยลำแสงอิเล็กตรอนสามารถรับความหนาแน่นของพลังงานได้มากกว่าแหล่งความร้อนที่มีความต้านทาน ซึ่งสามารถระเหยวัสดุที่มีจุดหลอมเหลวสูง เช่น W, Mo, Al2O3 เป็นต้น
②วัสดุเคลือบถูกใส่ไว้ในถ้วยใส่ตัวอย่างทองแดงที่ระบายความร้อนด้วยน้ำ ซึ่งสามารถหลีกเลี่ยงการระเหยของวัสดุต้นทางของการระเหยและปฏิกิริยาระหว่างกัน
③สามารถเพิ่มความร้อนลงบนพื้นผิวของวัสดุเคลือบได้โดยตรง ซึ่งทำให้ประสิทธิภาพเชิงความร้อนสูงและการสูญเสียการนำความร้อนและการแผ่รังสีความร้อนต่ำ
ข้อเสียของวิธีการระเหยด้วยความร้อนด้วยลำแสงอิเล็กตรอนคือ อิเล็กตรอนหลักจากปืนอิเล็กตรอนและอิเล็กตรอนทุติยภูมิจากพื้นผิวของวัสดุเคลือบจะทำให้อะตอมที่ระเหยและโมเลกุลของก๊าซตกค้างแตกตัวเป็นไอออน ซึ่งจะส่งผลต่อคุณภาพของฟิล์มในบางครั้ง
(3) การระเหยความร้อนด้วยการเหนี่ยวนำความถี่สูง
การระเหยด้วยความร้อนด้วยการเหนี่ยวนำความถี่สูงคือการวางเบ้าหลอมที่มีวัสดุเคลือบไว้ตรงกลางของขดเกลียวความถี่สูง เพื่อให้วัสดุเคลือบสร้างกระแสวนที่รุนแรงและเอฟเฟกต์ฮิสเทรีซิสภายใต้การเหนี่ยวนำของสนามแม่เหล็กไฟฟ้าความถี่สูง ซึ่งทำให้ ชั้นฟิล์มให้ร้อนขึ้นจนระเหยกลายเป็นไอแหล่งกำเนิดการระเหยโดยทั่วไปประกอบด้วยขดลวดความถี่สูงที่ระบายความร้อนด้วยน้ำและถ้วยใส่ตัวอย่างกราไฟต์หรือเซรามิก (แมกนีเซียมออกไซด์ อะลูมิเนียมออกไซด์ โบรอนออกไซด์ ฯลฯ)แหล่งจ่ายไฟความถี่สูงใช้ความถี่หนึ่งหมื่นถึงหลายแสนเฮิรตซ์ กำลังไฟฟ้าเข้าหลายถึงหลายร้อยกิโลวัตต์ ปริมาณของวัสดุเมมเบรนที่มีขนาดเล็กลง ความถี่ในการเหนี่ยวนำก็จะยิ่งสูงขึ้นความถี่ของขดลวดเหนี่ยวนำมักทำจากท่อทองแดงระบายความร้อนด้วยน้ำ
ข้อเสียของวิธีการระเหยความร้อนด้วยการเหนี่ยวนำความถี่สูงคือการปรับกำลังไฟฟ้าเข้าอย่างละเอียดนั้นไม่ใช่เรื่องง่าย แต่ก็มีข้อดีดังต่อไปนี้
①อัตราการระเหยสูง
②อุณหภูมิของแหล่งกำเนิดการระเหยนั้นสม่ำเสมอและคงที่ ดังนั้นจึงไม่ใช่เรื่องง่ายที่จะเกิดปรากฏการณ์ละอองของสารเคลือบกระเซ็น และยังสามารถหลีกเลี่ยงปรากฏการณ์รูเข็มบนฟิล์มที่เคลือบไว้
③โหลดแหล่งกำเนิดการระเหยเพียงครั้งเดียว และอุณหภูมิค่อนข้างง่ายและควบคุมง่าย
เวลาโพสต์: 28 ต.ค. 2565